Functional requirements of electric actuators For power plant valves
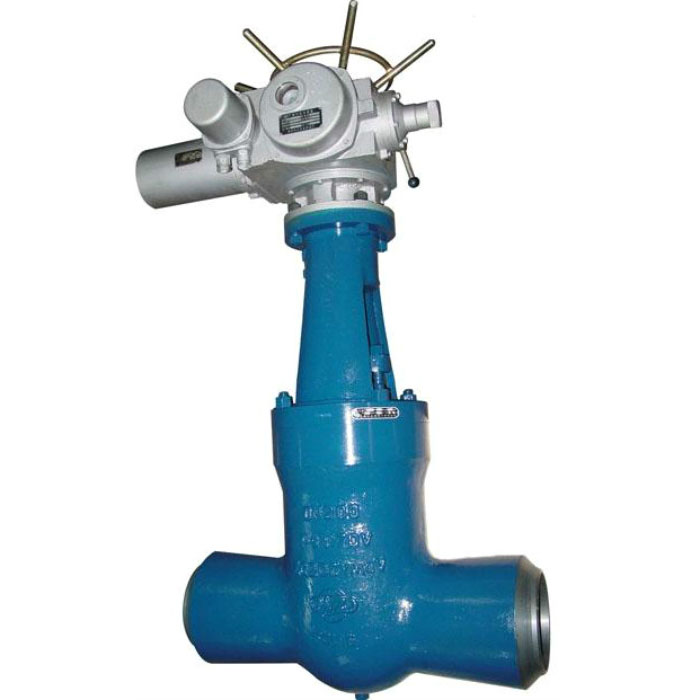
Valves for power station are mainly used to cut off or connect the pipeline medium. They have been widely used in the pipelines of various systems in thermal power stations and have attracted much attention. So what are implementation standards for the electric actuator of power station valves?
1. Protection class of electric device: indoors should not be lower than IP55 (without mechanical brake) and IP54 (with mechanical brake), and outdoor should not be lower than IP65.
1. When manual operation is performed on the electric actuator, the operating torque acting on the handwheel should not be less than 15Nm in case of the maximum control torque of the electric actuator. The structure of the handwheel (handle) should be able to withstand drive.
2. On-off electric actuators should have the following functions:
a) Output signals indicates full open, full close and at least one intermediate position;
b) When the load exceeds the maximum control torque, torque overload status signal shall be indicated in the opening and closing stroke directions;
c) output a long-distance flash signal indicating the state of movement;
d) Output the resistance signal or (4 ~ 20) mA DC current signal indicating the position of the American standard valve.
3. Adjustable electric actuators should have the following functions:
a) Output a status signal indicating the fully open and fully closed positions;
b) When the load exceeds the maximum control torque, output a torque overload status signal in the opening and closing stroke directions;
c) Output the (4-20) mA DC current signal indicating the valve position, and its load capacity should not be less than 650Ω;
d) The motor should be equipped with thermal protection elements.
4. The electric actuator with power control part should have the following functions:
a) The regulating electric actuator should be able to accept the following types of input signals:
1) (4 ~ 20) mA DC analog signal, the input impedance is not greater than 250Ω;
2) 24V DC pulse signal, pulse width is greater than 300ms;
3) Contact signal.
b) The switch-type electric actuator should be able to accept the following types of input signals:
1) contact signal;
2) 24V DC switching signal.
c) Achieve remote and local operation control and switch between remote and local.
d) The local operation control part must have protective measures to prevent misoperation.
e) Overcurrent protection of input power.
f) It should remain motionless when power is interrupted.
g) When the control signal is interrupted, it should remain motionless or return to a safe position.
6. Intelligent electric actuators should have the following functions:
a) All functions of electric actuator with power control part;
b) Parameter setting, debugging and fault diagnosis through the man-machine interface displaying various symbols, numbers and characters;
c) No dead-band oscillation under various operating conditions through dead zone adaptation or other methods;
d) prevent the motor from idling;
c) Automatic phase sequence correction of the input three-phase power;
f) When a fault occurs, it should stop at the original position and give a fault status signal;
g) Emergency operation of titanium valve closing and opening functions;
h) It has a fieldbus communication interface and meets the requirements of JB / T l0308.3.