Difference between fully welded ball valves for natural gas pipelines and other common valves
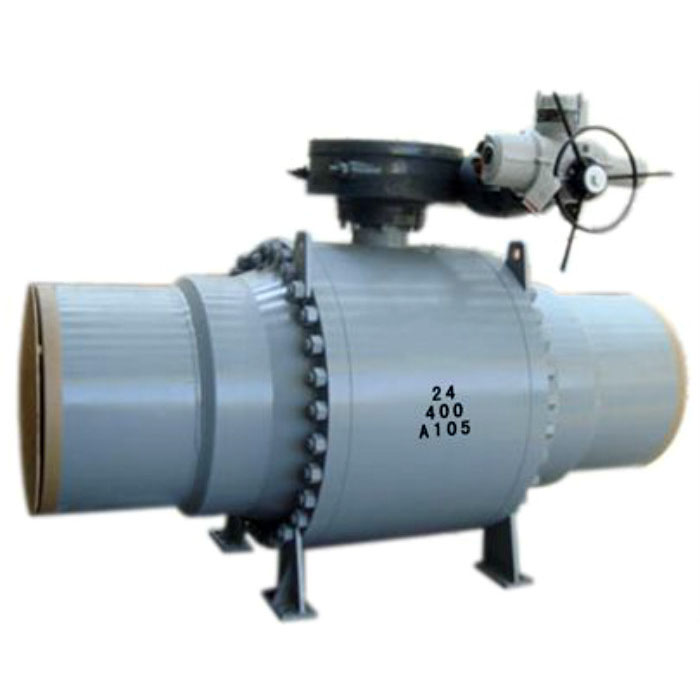
With the development of the natural gas pipeline industry, the amount of natural gas pipeline valves is increasing, and natural gas pipeline valves are different from other common valves. The specific difference are as follows:
1. Quick action and automatic shutdown
Because the management and control personnel are usually in the station or the central control room, it is required that the pipeline valve can be automatically cut off if a major accident such as a pipeline rupture occurs. The pipeline valve requires a small operating force, and can achieve accurate operation when the temperature and external force changes have an impact. In particular, the emergency shutdown ball valve must be fully open for a long period of time, and the pipeline must be quickly closed when necessary. At the same time, the valve opening and closing position and opening degree indicator are required to be accurate and easy to understand, and to meet the appropriate switching speed.
2. The output torque of the actuator is large and explosion-proof
Due to the high pipeline supply pressure, large caliber and fast switching time, the pipeline ball valve needs to adopt a high torque actuator, such as electric, pneumatic, gas-hydraulic or electro-hydraulic linkage. The drive must also have explosion-proof requirements, requiring EExdIIBT4, and protection class IP68.
3. Low leakage
Most natural gas pipeline networks are built on the edge of cities. They are not operated and managed in the way that workers often operate, maintain and inspect them. Generally, the city's natural gas pipelines are more than a hundred kilometers long, and can only be patrolled and inspected periodically. Sometimes the pipelines need to pass through areas with complicated conditions. The leakage of the medium may cause serious fire accidents. Especially for pipelines near the city, it is very important to prevent leakage of the valve.
Natural gas valve leakage requirements are very strict, usually buried and more important valves are all welded body structure. In order to ensure the sealing performance of pipeline valves, the sealing pair is required to have excellent corrosion resistance, wear resistance, self-lubricity and elasticity. In recent years, the development of polymer materials has provided a wide selection of materials for the selection of pipeline valve sealing materials, such as polytetrafluoroethylene, nylon, nitrile rubber (NBR), and special synthetic rubber (VITON).
4.Corrosion-resistant materials
Because the natural gas transported by the pipeline contains a large amount of hydrogen sulfide before desulfurization (this is a toxic and highly corrosive gas, it reacts with iron to form iron sulfide, which can peel off in flakes and penetrate mechanical equipment). Even if the natural gas is processed through desulfurization and other processes, there is still residual hydrogen sulfide. Therefore, the selection of pipeline valves should be corrosion-resistant and sulfur-resistant materials.
5.Long service life
Once the pipeline is put into operation, it is not allowed to stop operation for a few years. The longer the operation, the better. Unlike ordinary chemical plants or oil refineries, there is an overhaul period. The natural gas transported by the pipeline faces a large number of users in the entire city. There are residents, enterprises, factories, etc., especially enterprise users who use natural gas as raw materials, and there is no allowable interruption for a moment. If the pipeline valve connected in series to the pipeline fails, the consequences are unthinkable. Therefore, the main sealing and wearing parts of pipeline valves, such as valve seats, require long life. The service life of general trunk pipeline valves is more than 30 years.