How to choose valve trims?
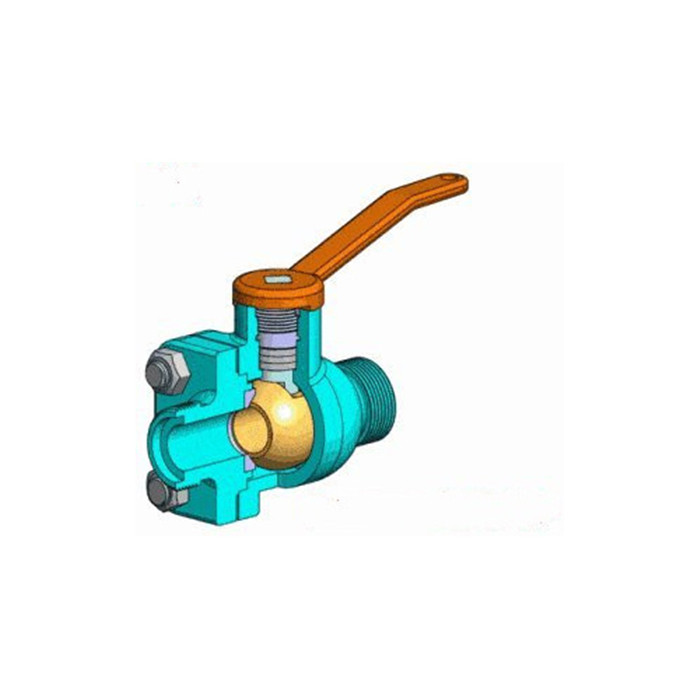
The internal parts of valves, or valve trims, mainly refer to the sealing surfaces of the valve stem, the disc , seat, the upper backseat, etc.
The selection principles of valve trims are comprehensively considered according to the condition of the main material, the characteristics of the medium, the structural characteristics, and the role and stress of the parts. For conventional general-purpose valves, valve trims have been specified in the standard or several materials have been specified by the designer according to specific circumstances. For some valves with special requirements, such as high temperature, high pressure, medium corrosion and other working conditions, you need to choose the valve trims according to the working conditions.
The opening and closing member is collectively called the part that cuts off or regulates the flow of media, such as disc, ball, etc. The sealing surface of the opening and closing member and the valve seat is the main working surfaces of the valve. Whether the material selection is reasonable directly affect the valve's function and service life.
As valves have a variety of applications, the working conditions of the valve sealing surface vary widely. The pressure can be from vacuum to ultra high pressure, the temperature can be from -269 ° C to 816 ° C, and some working temperatures can reach 1200 ° C. The working medium ranges from non-corrosive media to various corrosive media such as various acids and bases. From the perspective of the force on the sealing surface, it is squeezed and sheared. From the perspective of tribology, there are abrasive wear, corrosion wear, surface fatigue wear, erosion and so on. Therefore, the appropriate sealing surface material should be selected according to different working conditions.
(1) Abrasive wear
Abrasive wear refers to the wear that occurs when a rough hard surface slides on a soft surface. The hard material is pressed into the softer material surface, and a tiny groove will be drawn on the contact surface. The material falling off this groove is pushed away from the surface of the object in the form of debris or loose particles.
(2) Corrosive wear
When the metal surface is corroded, a layer of oxide is generated. This layer of oxide usually covers the affected part, which can slow down the further corrosion of the metal. However, if sliding occurs, the surface oxide will be removed, and the exposed metal surface will be further corroded.
(3) Surface fatigue and wear
Repeated cyclic loading and unloading will cause fatigue cracks on the surface or the subsurface layer, forming debris and pits on the surface, and eventually leading to surface damage.
(4) Erosion
The material's damage ring is caused by sharp particles colliding with the object. It is similar to abrasive wear, but the surface is rough.
(5) Scratches
Abrasion refers to the damage caused by friction during the relative movement of the sealing surface.