How to prevent packing leakage of stop valves
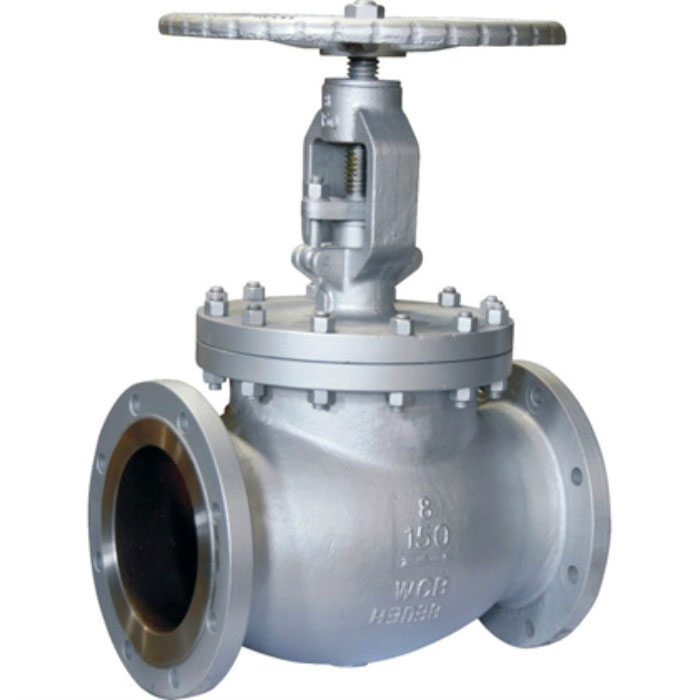
In the field maintenance, specific analysis and judgment should be made for the actual use of the valve, thereby fundamentally eliminating the cause of the leakage and solving the safety hazard.
According to the analysis of leakage, the main reasons are summarized as follows:
(1) The material and type of packing are not suitable:
If the PTFE packing is used in the working condition of 150°C-200°C, the creep will occur during long-term operation under critical conditions, and the sealing performance of the packing will be reduced by the action of high-pressure medium. For mediums with strong permeability such as liquid ammonia, tar, and fuel, braided packings are used. These conditions are affected by high-temperature and high-pressure media and are prone to leakage.
(2) Improper installation method of the packing:
After the packing is loaded into the stuffing box, the axial pressure is applied to the packing. Due to the plasticity of the packing, it generates radial force and is in close contact with the valve stem. When the packing is installed with uneven force to cause loosening, so the above contact is very uneven, causing the packing to leak.
(3) The interface leakage
The interface leakage between the valve stem and the packing is caused by the gradual attenuation of the contact pressure of the packing, the aging of the packing itself, loss of elasticity, etc., and the pressure medium leaks outward along the contact gap between the packing and the valve stem.
(4) Frenquent operation
After stop valves are frequently operated, the valve stem is easy to get bent, worn, corroded, and the smoothness is lowered, causing the packing to wear and leak.
(5) The stop valve changes during the working condition.
During the heating process of the equipment, the stop valve undergoes change from a cold state to a hot state. The hot medium changes greatly, and the valve stem is affected by the thermal expansion, so that the packing gap becomes larger. The packing leak is severe.
(6) The packing gland is not tight, skewed, or the horizontal installation.
They cause the valve stem to be in poor contact with the packing, and the gap becomes too large or too small.
How to prevent valve leakage:
(1) In order to facilitate the filling of the packing, chamfer the top of the stuffing box and place an erosion-resistant metal protection at the bottom of the stuffing box to prevent the packing from being pushed out by the medium pressure. The contact surface with the packing cannot be inclined
(2) Improve the surface precision and smoothness of the valve stem and stuffing box. If the friction coefficients between the various movable parts was zero, the force acting on the packing gland could be uniformly transmitted to the entire packing without any attenuation. The actual frictional forces is natureally present, so it is impossible to be zero, and the radial force acting on the packing decreases as the distance from the gland increases or decreases. The greater the frictional force, the greater the pressure decay. Once the sealed pressure exceeds the force on the packing, it begins to leak. Therefore, the stem and stuffing box should not be scratched, pitting and worn during maintenance, and the finish should be good.
(3) The selected materials must suit to withstand temperature changes, creep, relaxation or oxidation. In general, the conditions satisfy the preference for PTFE, and graphite is not satisfied. Mixed packings can also be used: one is a mixture of graphite packing and tetrafluoropacking; the other is a mixture of O-ring and V-type packing. Graphite packings can be used for the highly permeable medium.
(4) When packing, it should be added once in a circle, and pressed together one by one with a pressure tool, and pressed firmly to make the packing force uniform. The open packing should be placed 90° or 120° up and down. The number of packings to be added should be suitable for no leakage. Adding less packing gland will enter the stuffing box and cause leakage.
(5) For the PTFE packing acting as a spring, the gland screws should be tightened symmetrically and should not be skewed. Other types of packing do not have to be tightened too tightly so as not to leak.
(6) After the new stop valve or the stop valve that has just been repaired, the packing should be inspected for leaks. If there is any leakage, it should be treated in time to prevent the leakage of the packing from increasing.
Maintenance of packing during use
(1) When the forming packing is cut, a 45° slit is used, and each turn of the slit is 90° or 120° out of phase.
(2) Use PTFE forming packing under high pressure and pay attention to cold flow characteristics.
(3) The flexible graphite ring is used alone, and the sealing effect is not good, and should be used in combination with the graphite braided packing.
(4) Graphite packing can not be used for strong oxidants, such as concentrated sulfuric acid, concentrated nitric acid and other media.
(5) The dimensional accuracy, surface roughness, stem size accuracy and surface roughness of the stuffing box are the key factors affecting the sealing of the forming packing.
In many years of on-site practical applications, there are many reasons for packing leakage in the stop valve. As long as we are diligently observing and carefully analyzing causes of the leak, the problem of packing leakage can be eliminated; however, it should also be noted that some causes of packing leakage are complicated and there are many leakage factors. It is also necessary to continuously analyze and explore in future practical work.
If you are interested in more information, feel free to contact us via sales@jhflow.com