How to Select Industrial Valves in Chemical Piping Design
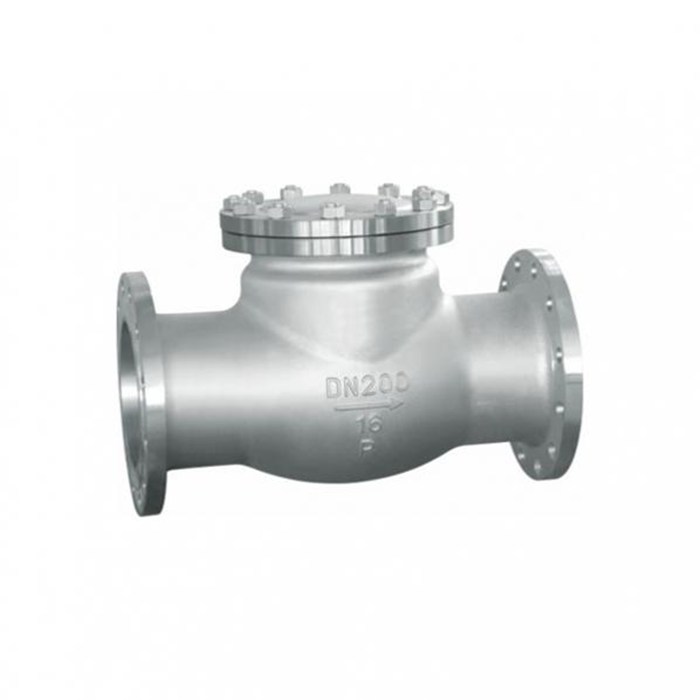
For chemical production, valves are one of the indispensable and important components. Whether their selection is correct and reasonable is directly related to the safety and stability of chemical production. As there are many types of valves, in chemical piping design, we should understand the characteristics of various commonly used valves and adopt scientific selection methods. Based on this point, this article first briefly describes the commonly used valve types in chemical piping design, and then discusses the valve selection methods in chemical piping design on this basis.
1 Commonly used valve types
1.1 Gate valves
This kind of valve is the most commonly used valve type in the design of chemical production equipment. When the gate valve is fully opened, the resistance coefficient to the fluid is the smallest, and the fluid will not change the flow direction when flowing through the valve. Compared with the globe valve, the gate valve has the characteristics of relatively small installation size, wide diameter range, and wide pressure and temperature range. It is the preferred valve type in chemical piping design.
1.2 Globe valves
This kind of valve is often installed in the part where the fluid flow needs to be adjusted, such as the pump outlet, the upstream of the regulating valve bypass flowmeter, etc. The globe valve mainly adjusts the flow rate by moving the closing member along the center line of the valve seat, but its function is not equivalent to the throttle valve. Compared with the gate valve, the globe valve generates less friction during operation and has good wear resistance; the globe valve has only one sealing surface, which has good sealing effect and convenient maintenance; the opening height of the globe valve is small.
1.3 Check valves
Check valves, or non-return valves, refer to valves that only allows fluid to flow in a single direction, and does not allow fluid to flow back to the original path. In the case of fluid flow, the valve flap of the check valve automatically opens; in the case of fluid flow backward, the valve flap of the check valve automatically closes.
1.4 Butterfly valve
The butterfly valve has simple structure, small size, low weight, and relatively small resistance to the fluid. However, the opening and closing operation of the butterfly valve is flexible, and it has good performance in flow adjustment. Under normal circumstances, butterfly valves are mainly used in parts with large pipe diameters, low fluid pressure, and rapid opening and closing requirements.
1.5 Plug valve
This kind of valve has the characteristics of good sealing, strong durability, flexible opening and closing, and it is not easy to accumulate fluid in the cock valve cavity, and will not pollute other materials, so it is suitable for high-risk fluid control, or in special Occasion use. However, due to the large opening and closing torque of the plug valve, its cost is high.
1.6 ball valve
This type of valve is developed on the basis of the plug valve, which has similar functions to the plug valve, but is cheaper than the plug valve. Among all valve types, the ball valve has the best fluidity and tightness, and is easy to maintain, small in fluid resistance, flexible in opening and closing operations, and has a broader scope of application.
2 Valve selection method in chemical piping design
2.1 Correctly select the type of valve
In the chemical piping design, the valve type should be selected correctly according to the actual situation. In actual production, different valve types have different effects on chemical production, and their characteristics and applicable performance may be different, so the valve type must be selected according to the needs of chemical production. The chemical piping designer must fully understand the chemical production process and the operating conditions where the valve is installed, and also grasp the performance and scope of application of various types of valves, and predict the problems that the valve may encounter during installation and use, based on this Select the valve type. Different types of valves have different functions. It is necessary to solve the pressure problem of switch operation according to the needs of chemical production links, so that the valve selection is more targeted.
2.2 Reasonably determine the end connection of the valve
In the process of valve selection, it is necessary to fully grasp the applicability of the valve. It is necessary to select the applicable valve and handle the connection of the valve end, so that the overall installation of the valve can meet the needs of chemical production. The valve end connection includes welding end, thread, flange connection, the latter two are common connection methods. Threaded connection is suitable for the connection of valves with a diameter not exceeding 50mm. If this standard is exceeded, the airtightness of the valve will be reduced and the overall installation effect of the valve will be affected; flange connection is suitable for the connection of diameter and pressure pipes, and is the same as threaded connection Compared with, although its installation and disassembly are simple and convenient, the flange connection is relatively heavy and the installation cost is relatively high; welding can be adopted when the thread connection and flange connection are not applicable, although this connection method is highly reliable , Can play a more sealing role, but it is not easy to disassemble and is not conducive to maintenance.
2.3 Clarify the specific function of the valve
chemical piping designers must clearly understand the basic functions of different types of valves and the role that valves can play in chemical plants. In the chemical piping design, the designer should understand the operating requirements of the chemical plant, the nature of the fluid in the pipeline, grasp the requirements of the fluid medium characteristics, temperature changes, and pressure capacity on the valve, and select the appropriate valve according to the specific operation mode of the chemical production. Ensure that the specific functions of the valve can be fully utilized. At the same time, it is necessary to consider the economic cost of valve installation, not only to ensure the function of the selected valve type, but also to ensure that the cost is reasonable.
2.4 Preferred valve material
In the selection of valve type, the material of the valve must be strictly controlled. This is an important prerequisite to ensure the service life and function of the valve. When selecting the valve housing, internal components, and sealing surface materials, it is necessary to understand the working environment of the valve, including medium pressure, temperature, physical properties, chemical properties, and flow direction requirements. Especially for corrosive media, it is necessary to select corrosion-resistant valve materials in accordance with relevant specifications, so as to ensure the cleanliness of the media itself, and can not be mixed with solid particles of valve materials that are corroded by the media. Common valve materials include ductile iron, low-alloy steel, malleable cast iron, gray cast iron, austenitic stainless steel, ceramics and other materials. When selecting valve materials, both the economy of the valve and the service life and use of the valve must be taken into consideration. Performance to ensure the normal function of the valve during use.
3 Conclusion
In summary, in chemical piping design, valve selection is a relatively important task. Due to the large number of valve types, if the selection is wrong, it will have a certain impact on chemical production. For this reason, valve selection must be carried out correctly. Only in this way can the valve's role be maximized, so as to ensure the safe and stable progress of chemical production, which has important practical significance for improving the economic benefits of chemical enterprises.